-
-
-
Total payment:
-
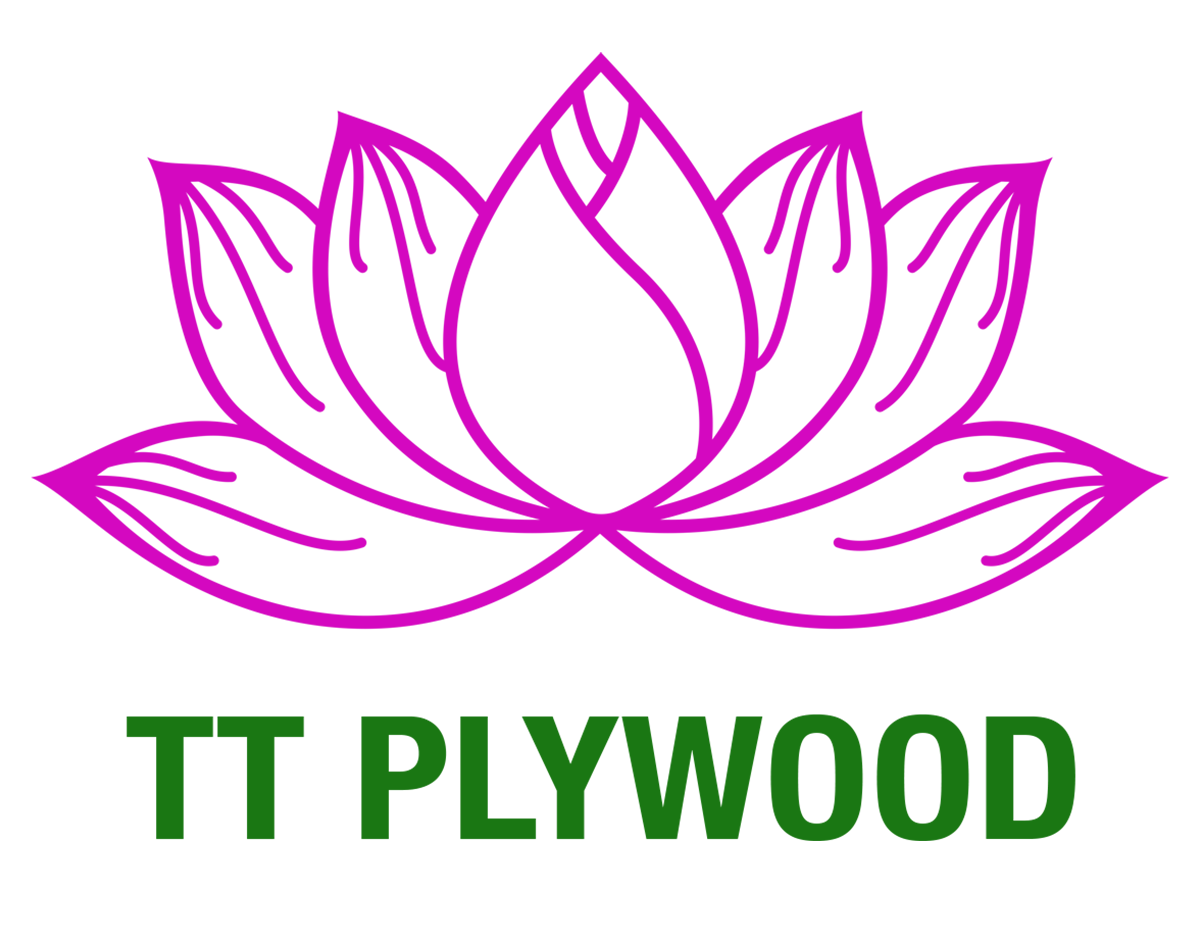
Birch Plywood Production Process: From Log to Premium Panel
Posted by Thanh Uyên at 07/07/2025
Scroll down to see real photos and behind-the-scenes videos from our production line at TT Plywood from raw logs to final panels. Birch plywood is widely appreciated for its durability, stability, and smooth surface, making it a popular choice in furniture, interior design, and structural applications. This guide walks you through the entire birch plywood production process from preparing veneers to hot pressing and final finishing. Whether you're part of the wood industry or simply looking to learn more, this article offers a detailed, step-by-step look into how quality birch plywood is made.
Overview of the Production Process
At TT Plywood, the birch plywood production process follows a clear and systematic approach, ensuring quality at every step. From carefully selected raw materials to precise manufacturing and inspection, here is how each stage contributes to creating high-performance plywood:
1. Raw Materials: Sustainable Birch Logs
The process begins with responsibly harvested birch trees (Betula pendula) from well-managed forests. Only high-quality logs—those with the right diameter, clean grain, and minimal defects—are selected to ensure strong and reliable plywood.
2. Log Handling & Debarking
Logs are delivered to the mill and soaked in log ponds to maintain moisture, which makes debarking easier. Powerful de-barking machines remove the outer bark before the logs are cut to size for the peeling stage.
3. Rotary Peeling: Creating Birch Veneer
The prepared logs are fed into rotary lathes, where they are spun and peeled into thin sheets of birch veneer. These layers, usually 1/16″–1/8″ thick, are the building blocks of the plywood’s strength and appearance.
4. Grading & Sorting Veneers
Once peeled, veneers are sorted either by machine or by hand. They are classified into:
- Face-grade: top-quality sheets used for the outer surfaces.
- Core-grade: slightly lower-grade sheets used in the inner layers.
Proper grading ensures consistency and performance in the final product.
5. Veneer Drying
Fresh veneer sheets contain high moisture levels. They are dried in industrial machines to reduce moisture content to around 6–10%, helping prevent defects like warping or delamination.
6. Adhesive Application & Lay-Up
After drying, veneers are coated with waterproof adhesives. Exterior plywood usually uses phenol-formaldehyde glue, while interior types use urea-formaldehyde. The veneers are then stacked with alternating grain directions (cross-grain) for added strength.
7. Hot Pressing & Plywood Press
The veneer stack is pressed using high heat and pressure (about 140°C), curing the adhesive and bonding the layers into a single, solid sheet. Cold pressing may also be used in certain non-structural applications to save energy.
8. Trimming, Sanding & Quality Inspection
Pressed panels are cut to standard sizes (like 4×8 ft or 1220×2440 mm) and sanded smooth. Automated systems and trained inspectors check for strength, moisture resistance, and compliance with quality grades.
9. Grading & Certification
Finished panels are assigned grades (A, A/B, B/BB, etc.) based on surface quality and strength. Trusted manufacturers also obtain certifications such as FSC, PEFC, or CARB, ensuring environmental responsibility and consistent product quality.
10. Packaging & Distribution
Final plywood panels are packed securely and prepared for shipment. Good packaging helps protect against moisture and damage, ensuring the product arrives in excellent condition.
Why Birch Plywood? Key Advantages
- Strength & Stability: Cross-laminated structure resists bending and warping.
- Smooth Appearance: Clean, light-colored grain makes it suitable for visible finishes.
- Long-lasting: Resistant to moisture and wear, especially with high-quality adhesives.
- Sustainable Choice: Certified sourcing supports eco-friendly building practices.
Common Applications of Birch Plywood
Thanks to its versatility and strength, birch plywood is used in a wide range of industries:
- Furniture: Ideal for sturdy chairs, tables, beds, and shelves.
- Cabinetry: Perfect for clean cuts and professional-looking edges in kitchens and bathrooms.
- Interior Design: Great for wall panels, built-ins, and ceiling features.
- Flooring Base Layers: Offers a reliable foundation for engineered flooring.
- Vehicles & Transport: Lightweight and durable, used in RVs and trailers.
- Packaging: Strong enough for crates, boxes, and reusable containers.
- CNC & Precision Cutting: Even thickness and smooth finish make it CNC-friendly.
- Acoustic & Soundproof Panels: Adds both structure and acoustic performance.
Market Trends & Outlook
Global demand for birch plywood is on the rise, fueled by trends in green building, custom furniture, and efficient construction. Technological advancements in adhesives, CNC cutting, and waste reduction are also pushing the industry forward.
Conclusion
Knowing how birch plywood is made helps buyers and professionals appreciate what sets premium panels apart. Every step from rotary peeling to pressing and grading plays a key role in creating a dependable product. At TT Plywood, we combine state-of-the-art technology with sustainable practices to deliver high-performance, eco-friendly solutions to clients around the world.
Looking for a trusted birch plywood supplier? Contact TT Plywood today to request a quote, schedule a factory visit, or learn how we can support your next project with high-quality, sustainable solutions.
Hotline/WhatsApp/Line/Kakao: +84 326 942 288
Email: info@ttplywood.com
Website: https://ttplywood.com/
LinkedIn: TT PLywood
Frequently Asked Questions (FAQ)
What is the difference between birch plywood and Baltic birch plywood?
While both are made from birch veneers, Baltic birch plywood typically refers to panels manufactured in Northern Europe, especially around the Baltic Sea region. It is known for having more plies, a thicker core, and no filler layers — resulting in greater strength and stability. Standard birch plywood may have fewer plies and could include mixed hardwood cores. At TT Plywood, we apply similar quality standards found in Baltic birch to ensure high performance and consistency.
Is birch plywood waterproof?
Birch plywood can be water-resistant, especially when bonded with phenol-formaldehyde adhesive. However, it is not 100% waterproof unless specifically treated or manufactured for exterior or marine-grade applications.
Can birch plywood be used outdoors?
Exterior-grade birch plywood, manufactured with waterproof glue and sealed edges, can be used in outdoor settings. For prolonged outdoor exposure, marine plywood or specially treated panels are recommended.
What thicknesses are available for birch plywood?
Birch plywood is available in a wide range of thicknesses — commonly from 3mm to 25mm. Custom thicknesses can also be produced depending on application and order volume.
Is birch plywood suitable for laser cutting or CNC routing?
Yes. Birch plywood is widely used for laser cutting and CNC machining because of its uniform thickness, minimal voids, and clean finish.