-
-
-
Total payment:
-
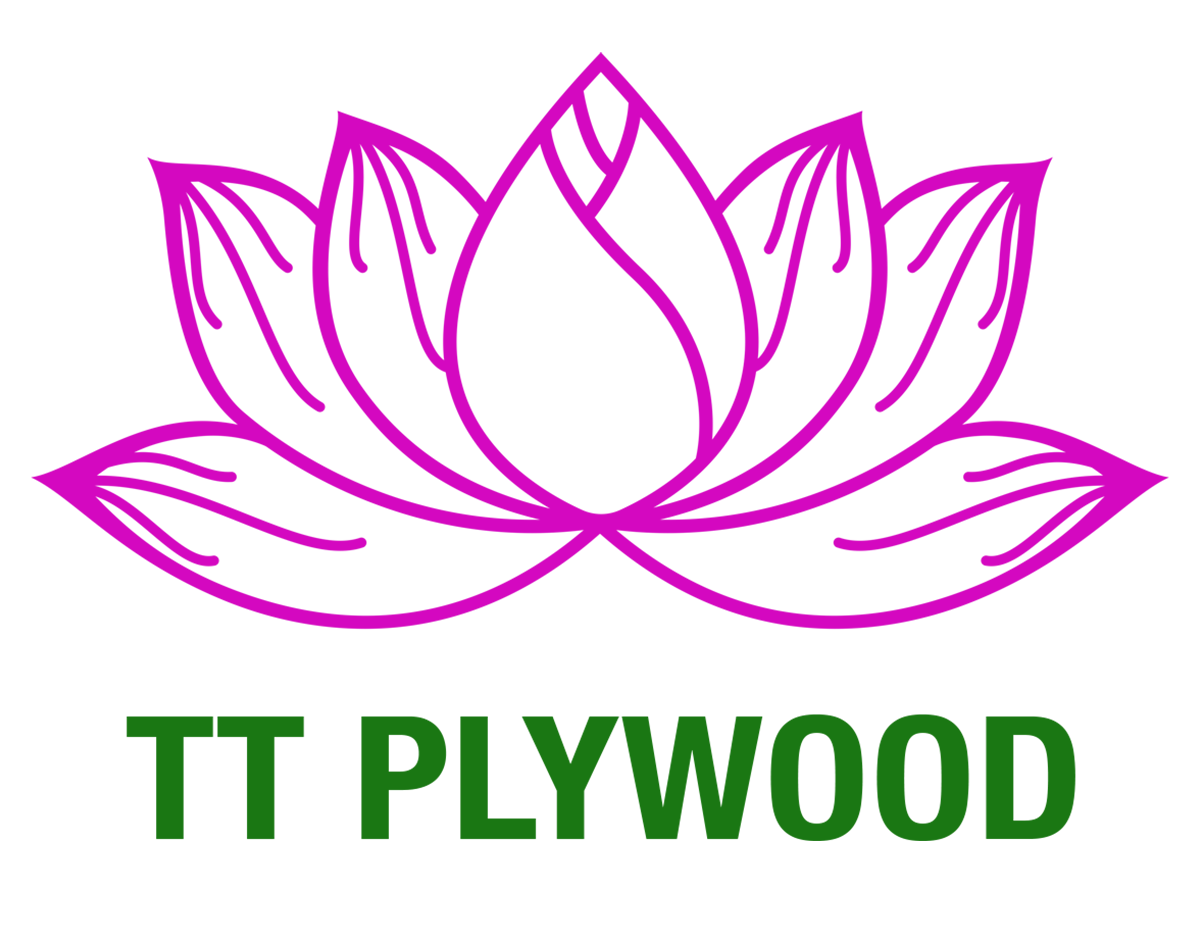
Can Waterproof Film-Faced Plywood & LVL Revolutionize Your Projects?
Posted by Thanh Uyên at 15/07/2025
When your readers finish reading your article "Waterproof Plywood – The Ultimate Solution for Durable Construction," the next natural question is: which specific plywood products are actually performing best in real-world construction and modular applications?
The answer: Film-Faced Plywood and Laminated Veneer Lumber (LVL). These two engineered wood materials are seeing a surge in demand across Europe and the United States, not only because of their durability, but because they meet modern needs for sustainability, water resistance, and modular flexibility.
Film-Faced Plywood: The Waterproof Backbone of Modern Construction
Film-faced plywood is one of the most widely used and tested materials in outdoor construction. It consists of a plywood core (usually hardwood or poplar) coated with a phenolic or melamine film that creates a smooth, waterproof surface.
In the EU and US, film-faced plywood has gained significant popularity due to its excellent water resistance, making it ideal for concrete formwork and wet environments. Its smooth surface finish ensures clean separation from concrete molds, while its durability allows for multiple reuses—high-quality sheets can be used 15 to 20 times. These benefits have made it a preferred material in modular and precast systems, particularly in Europe, where sustainable construction is increasingly prioritized.
Use Cases:
- Concrete formwork
- Temporary road surfacing
- Scaffolding platforms
- Precast housing panels
Buyers in the EU and U.S. are also looking for eco-friendly phenolic coatings and FSC-certified cores, further pushing demand for high-standard film-faced products. Contact our TT Plywood supporter to know more about what will fit most on your project in here.
Laminated Veneer Lumber (LVL): Structural Strength Meets Moisture Resistance
LVL is an engineered wood product made by layering thin sheets of wood veneer, glued together under heat and pressure. When bonded using WBP (Weather and Boil-Proof) glue, it becomes highly resistant to moisture and suitable for semi-exterior structural use.
LVL is gaining attention for its incredible strength-to-weight ratio, making it stronger than solid wood and more uniform. It maintains straightness and consistency, avoiding the warping and twisting common in traditional timber. Its moisture resistance, especially when bonded with WBP glue, allows it to perform well in humid environments. These properties have made LVL increasingly popular in mass timber and modular structures across both Europe and North America.
Use Cases:
- Beams and headers in prefab housing
- Rim boards, joists, and load-bearing walls
- Framing for container homes and tiny houses
- Structural components in passive homes
LVL is not fully waterproof like marine plywood but offers reliable moisture resistance when sealed and installed correctly.
Key Differences at a Glance
Feature | Film-Faced Plywood | LVL (WBP Bonded) |
---|---|---|
Water Resistance | Excellent (film + phenolic glue) | Very good (WBP glue) |
Primary Uses | Concrete formwork, modular panels | Structural framing, prefab builds |
Mechanical Strength | Medium-High | Very High |
Reusability | High (15–20 uses) | Built-in permanent structures |
Market Demand | Mature | Emerging in prefab/mass timber |
Both materials serve different yet complementary roles. Film-faced plywood thrives in exterior-facing temporary roles, while LVL offers long-term strength in structural design. Is Plywood Waterproof?
Waterproof Performance: What Buyers Should Know
To be classified as waterproof or water-resistant, both products must use:
- Phenolic or WBP glue: Ensures bond strength even after boiling water tests.
- Protective edges/sealants: Especially on LVL ends to prevent water ingress.
- Verified thickness and core quality: Cheap variants may contain voids that compromise durability.
In export markets like Europe, CARB, CE marking, FSC, and EUTR compliance are non-negotiable. U.S. buyers increasingly ask for fire-rated, low-emission plywood, and verified origin documentation.
Market Momentum: Where Waterproof Plywood is Going
The waterproof plywood market is experiencing strong momentum globally. In Europe, there is a growing adoption of LVL in mass timber architecture, driven by a focus on sustainability and energy-efficient buildings. Film-faced plywood remains in high demand for concrete formwork, especially in large-scale infrastructure projects that require durability and reusability.
Meanwhile, the United States is witnessing a resurgence in infrastructure spending and a boom in prefab housing. These trends, coupled with increasing occurrences of extreme weather, have pushed the demand for moisture-resistant engineered wood to new heights.
Globally, the market for waterproof engineered plywood including film-faced plywood and WBP-bonded LVL—is expected to grow at a CAGR of 5.5%, with LVL standing out as one of the fastest-growing segments.
Final Tips for Choosing the Right Waterproof Product
- Know your end-use: Film-faced is better for exposed, temporary jobs. LVL works for permanent framing.
- Ask for bonding specs: WBP or phenolic glue is essential.
- Request technical data: Especially load ratings, reusability, and tolerance levels.
- Don’t forget certification: FSC, CE, CARB, EUTR = buyer trust.
- Test samples: Especially if sourcing from a new supplier or country.
TT PLYWOOD supplies both high-reuse film-faced plywood and WBP-bonded LVL to global buyers. With FSC-certified cores, in-house inspections, and tailored specifications, we help buyers stay compliant while building faster and smarter.
Want to request product data sheets or see export-ready samples? Contact us at TT Plywood or:
Hotline/WhatsApp/Line/Kakao: +84 32 694 2288
Email: info@ttplywood.com
Website: https://ttplywood.com/
Frequently Asked Questions (FAQ)
Q1: Are film-faced plywood and LVL fully waterproof?
Film-faced plywood is highly water-resistant due to its phenolic coating and glue, making it suitable for repeated outdoor use. LVL, when bonded with WBP glue and properly sealed, offers reliable moisture resistance, though not as waterproof as marine plywood.
Q2: Can these products be used in exterior structural applications?
Yes. Film-faced plywood is ideal for concrete formwork, while WBP LVL can be used in beams, frames, and other structural elements, especially when sealed and protected.
Q3: How many times can film-faced plywood be reused?
High-quality film-faced plywood can be reused 15–20 times, depending on how well it’s handled and maintained.
Q4: Do I need certifications like FSC or CE for exporting to EU or US?
Absolutely. Certifications such as FSC, CE, CARB, and EUTR compliance are increasingly required by buyers in the EU and U.S. markets.