-
-
-
Total payment:
-
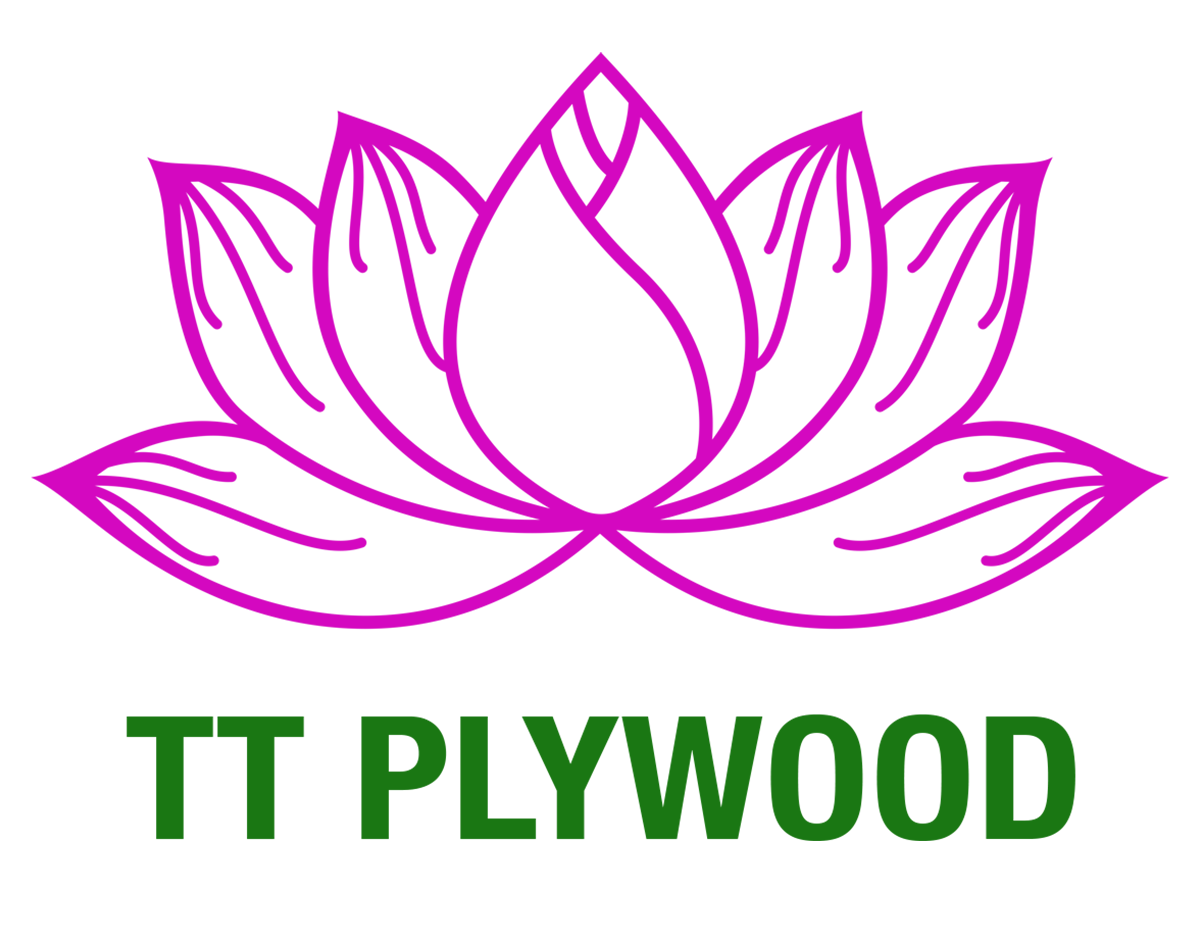
Vietnam Melamine Plywood: Production Process & Export-Grade Quality Explained
Posted by Đỗ Tiến Hải at 30/09/2024
Melamine plywood is one of the most widely used materials in the modern furniture and interior design industry. Thanks to its smooth surface, excellent moisture resistance, and cost-efficiency, it has become a top choice for manufacturers across Europe, North America, and the Middle East. However, not all melamine boards are made equal. The key lies in a rigorous production process, from core veneer selection to 100% final inspection.
At TT Plywood, one of Vietnam’s leading plywood manufacturers, melamine-faced plywood is produced through a 20-step quality-driven workflow. This article provides an in-depth look into the melamine plywood production process, helping buyers understand how consistency, durability, and aesthetics are achieved.
Melamine Plywood Production Process
🌿 What Is Melamine Plywood?
Melamine plywood is a type of decorative plywood that features a melamine-impregnated paper layer bonded to the plywood surface. This provides:
- A ready-to-use, sealed surface
- Resistance to scratches, moisture, and stains
- A wide range of design options: wood grain, matte, glossy, solid color
It’s commonly used in wardrobes, kitchen cabinets, office furniture, retail displays, and other indoor applications.
Step-by-Step Melamine Plywood Production Process
1 Selecting the core veneer
The production begins with inspecting each veneer sheet individually. Only Grade A core veneers (typically acacia or eucalyptus) with flat surfaces and no holes are selected for high-end applications. For more budget-friendly options, Grade B veneers may be used internally, but always paired with Grade A for outer layers.
Key advantage: This manual grading ensures strength and uniformity from the inside out.
Selecting the core veneer
2. Sanding the edge
Short edges of each veneer are sanded to allow tighter alignment during lay-up. This step prevents overlaps and ensures an even core thickness, especially important for CNC machining.
Sanding the edge
3. Gluing the core veneer
We use E0 or CARB P2-certified glue – a low-emission adhesive compliant with global health and safety standards. Glue is mixed with flour and dye, then evenly applied via a glue spreader to both sides of each veneer.
Gluing the core veneer
4. Arranging the core veneer
Veneers are stacked in alternating dry and wet layers to ensure optimal bonding. Plastic staplers are used to fix the layout, minimizing shifting before pressing.
Arranging the core veneer
5. Cold Pressing
The core stack is cold-pressed under high pressure for 4–8 hours depending on the humidity and thickness. This step pre-bonds the core and gives it a preliminary shape.
Cold - pressing the core
6. Repairing the core
Workers remove excess veneer, patch any surface gaps, and flatten overlapping areas. The core must be defect-free before hot pressing.
Repairing the core
7. Cutting
The pre-pressed panel is cut to remove outer edge irregularities, ensuring clean edges and dimensional accuracy.
8. Hot pressing the core
The core sheet will be put into the hot press machine, one tray for one sheet, ensuring flat boards and quite accurate thickness.
The hot-pressing time depends on every thickness & the weather condition for about 20 to 50 minutes. for example 25 minutes with 15mm, 40 minutes with 20mm,…
The high pressure and suitable temperature is set up by our experienced workers, which helps bond the veneer layers together and permanently solidify the product
Hot pressing the core
9–10. Surface Puttying & Dual Sanding
Putty is used to fill tiny gaps and uneven spots. After natural drying (3–4 days), boards are sanded twice to ensure a smooth and uniform surface before the face lamination stage.
11. Gluing the core
A thin protective glue layer is applied to the sanded core surface to prevent the inner core from showing through after melamine lamination.
12. Check the surface of the core
Any visible holes or surface defects are patched. The panel must be fully smooth, clean, and flat before facing.
13. Gluing and pasting the face
After the core is checked, it will be coated with glue in order to put the face veneer. The glue used is the same as the glue we used to bond the core. The faces are carefully put on the glue coated core.
Gluing and pasting the face
14. Hot-pressing the face
At approx. 110–120°C and high pressure, the face layer is bonded in 6–7 minutes. This creates a durable and visually appealing melamine surface.
Hot-pressing the face
15- 16. Final Cutting & Face Repair
Panels are trimmed to standard sizes (usually 1220×2440mm). Workers inspect the face veneer for chips or bubbles and repair any flaws using adhesive and patching.
17. Final Sanding
Light sanding gives the panel a smooth and slightly glossy finish, ready for direct use in furniture production.
18. 1-by-1 Manual Inspection
Every board is inspected individually by TT Plywood’s trained QC team. Checks include:
- Size and thickness accuracy
- Surface finish and defects
- Edge integrity
- Moisture content
- Tap test for internal delamination (for 11mm+ boards)
This level of quality control is rare in the industry and key to our reputation in furniture-grade plywood for export.
Inspection
19–20. Packaging & Loading
Boards are bundled with carton protection and steel straps, placed on pallets, and stored in dry warehouses before loading into shipping containers.
Packaging
Loading
Here is the production process of melamine plywood by TT PLYWOOD.
Why TT Plywood Stands Out in the Global Market
- Fully transparent production – with images, videos & live inspections upon request
- 100% manual inspection – before packing, not just random sampling
- Flexible customization – face color, finish (matte/glossy), size, glue, core type
- Certified glue – E0, CARB P2, ISPM-15 heat treatment available
- Optimized for CNC cutting – thanks to smooth surface and tight tolerance
Ideal Applications for Melamine Plywood
- Flat-pack furniture
- Closets, wardrobes & cabinets
- Office desks and dividers
- Retail shelving & interior partitions
- Wall paneling and modular systems
❓ Frequently Asked Questions
Q: Is melamine plywood waterproof?
It is water-resistant, suitable for indoor furniture, but not recommended for direct outdoor exposure unless specially treated.
Q: Can you provide FSC-certified melamine plywood?
Yes. We offer FSC options on request, especially for EU clients requiring traceable supply chains.
Q: How do you ensure no core exposure?
We apply anti-core glue and perform dual surface inspections before and after face pressing.
______________________
📩 Contact TT Plywood
Looking for a reliable melamine plywood supplier from Vietnam?
Let our team assist you with samples, prices, and expert advice.
📧 Email: info@ttplywood.com
📞 WhatsApp/Line/Zalo: +84 326 942 288
🌐 Website: https://ttplywood.com