-
-
-
Total payment:
-
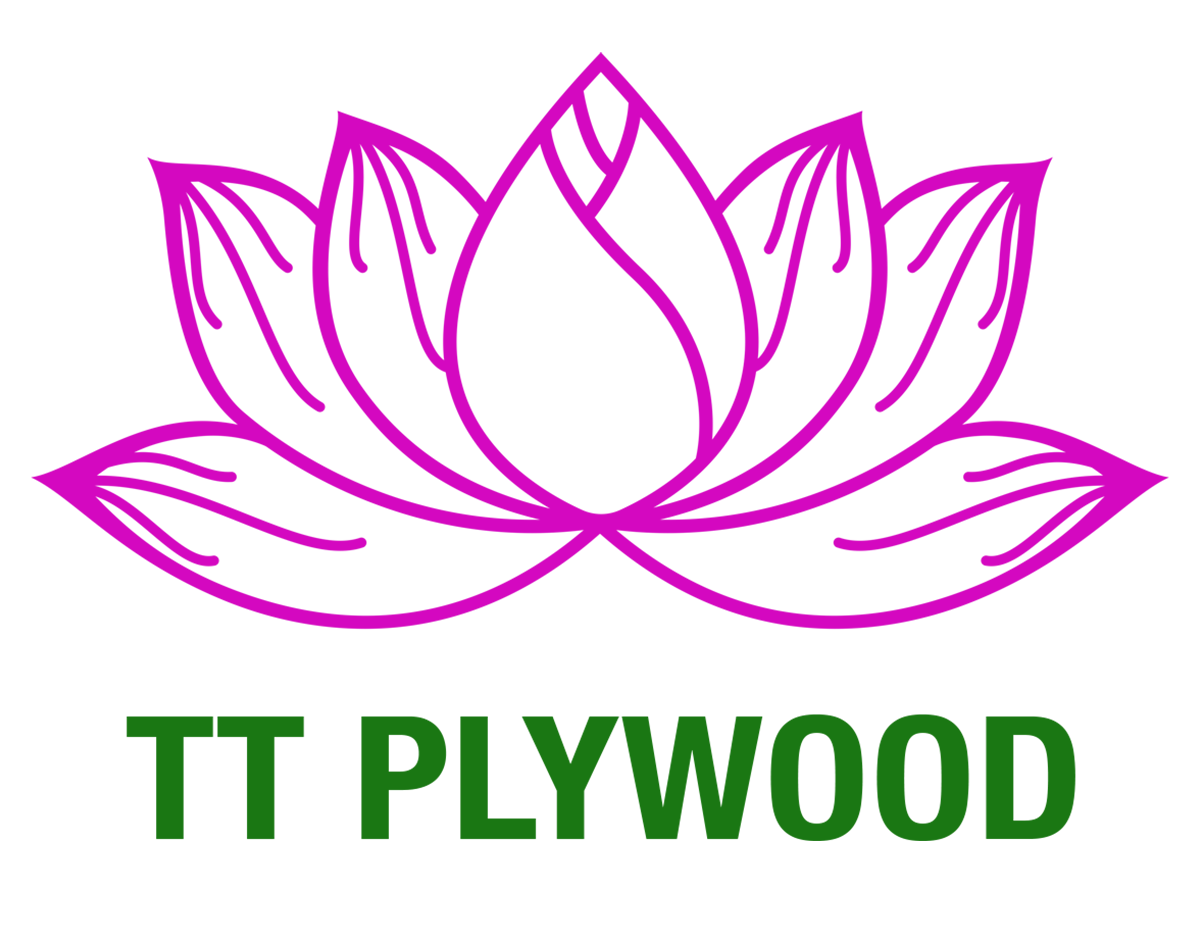
CNC-Ready Plywood: What Importers Should Look For in 2025
Posted by Thanh Uyên at 08/04/2025
Introduction
The global plywood market is evolving rapidly, and CNC (Computer Numerical Control) machining is becoming a game-changer for furniture makers, cabinetry manufacturers, and construction firms. If you're importing plywood in 2025, you need to ensure your material is CNC-ready—meaning it cuts cleanly, holds precision, and minimizes waste.
But what exactly makes plywood CNC-compatible? And how do you choose the right supplier? This guide breaks down the key factors importers must consider, from core composition to moisture resistance, helping you make smarter buying decisions.
1. What is CNC-Ready Plywood?
CNC machines use high-speed routers to cut, drill, and shape plywood with laser-like precision. However, not all plywood performs well under CNC machining. Poor-quality plywood can lead to:
- Chipping & Tear-out – Rough edges ruin finish quality
- Tool Wear – Dull blades increase production costs
- Warping – Inconsistent thickness affects assembly
CNC-ready plywood is specially engineered to avoid these issues. It has:
- Tight, void-free cores (no gaps between layers)
- High-density face veneers (clean cuts without splintering)
- Stable moisture content (8-10%) – Prevents warping post-machining
2. Key Features to Look for in 2025
A. Core Material: The Backbone of CNC Performance
Not all plywood cores are equal. The best options for CNC work:
- Poplar Core – Lightweight, stable, and cost-effective (great for furniture)
- Birch Core – Denser, stronger (ideal for high-precision cabinetry)
- Multi-Layer Hardwood – Best for heavy-duty applications (e.g., architectural millwork)
❌ Avoid: Low-grade mixed hardwood cores—they often contain voids that cause CNC bits to deflect.
B. Face Veneer Quality: Smooth Cuts, Flawless Finish
The outer veneer determines how cleanly the CNC machine cuts. Look for:
- A-grade faces (no patches, minimal knots)
- Sanded surfaces (helps with laser-guided CNC alignment)
- Consistent thickness (±0.2mm tolerance)
✅ Pro Tip: If your CNC project requires painting, opt for B/BB-grade faces—they’re cheaper but still machine well.
C. Moisture Content: Stability is Everything
Plywood with high moisture content (12%+) will warp after machining, ruining precision. The sweet spot:
✅ 8-10% MC (Moisture Content) – Stable for indoor use
✅ 6-8% MC – Best for high-humidity environments
How to verify? Ask suppliers for third-party moisture test reports (e.g., SGS).
D. Glue Quality: No Delamination Under High-Speed Cutting
Cheap urea-formaldehyde glue breaks down under CNC heat, causing layers to separate. Instead, look for:
- Phenol-formaldehyde (WBP glue) – Waterproof and heat-resistant
- E0/E1 certification – Low formaldehyde (safer for indoor use)
3. Emerging Trends in CNC Plywood (2025 Update)
A. Pre-Laminated Plywood (Saves CNC Time)
More suppliers now offer pre-finished plywood (melamine, HPL, or PVC-coated). Benefits:
- No post-CNC painting needed – Faster production
- Scratch-resistant surfaces – Better durability
B. Digital Grading & Traceability
Leading mills now use AI scanning to:
- Detect internal voids before shipping
- Assign unique QR codes for batch tracking
C. Sustainable Sourcing (EUDR Compliance)
New EU Deforestation Regulation (EUDR) requires proof that plywood isn’t from illegal logging. Ensure your supplier provides:
- FSC/PEFC certification
- Geolocation data of timber sources
4. How to Test CNC-Ready Plywood Before Buying
Step 1: Request Samples
- Have your CNC operator test-cut them
- Check for clean edges, no tear-out
Step 2: Verify Certifications
- FSC/PEFC (Sustainable sourcing)
- CARB Phase 2 (Low formaldehyde)
- JAS (for Japanese buyers)
Step 3: Audit the Factory (If Possible)
- Inspect storage conditions (moisture-controlled warehouses?)
- Check production logs for consistency
5. Where to Source Reliable CNC Plywood in 2025
Best Regions for Importers:
- Vietnam – High-quality birch plywood at competitive prices
- Finland/Russia – Premium Baltic birch (ideal for precision work)
- Indonesia – Cost-effective options for budget projects
Red Flags in Suppliers:
❌ No moisture test reports
❌ Unwillingness to provide small samples
❌ Vague answers about core composition
Conclusion: Smart Buying = Fewer Headaches
Choosing CNC-ready plywood in 2025 isn’t just about price—it’s about reducing waste, improving efficiency, and ensuring long-term durability. By focusing on core quality, moisture stability, and certifications, importers can avoid costly mistakes and keep their CNC operations running smoothly.
Need help finding a trusted supplier? Contact us for verified CNC-grade plywood manufacturers with full documentation.
📞Hotline/WhatsApp/Line/Kakao: +84 32 694 2288
📧Email: info@ttplywood.com
🌐Website: https://ttplywood.com/