-
-
-
Total payment:
-
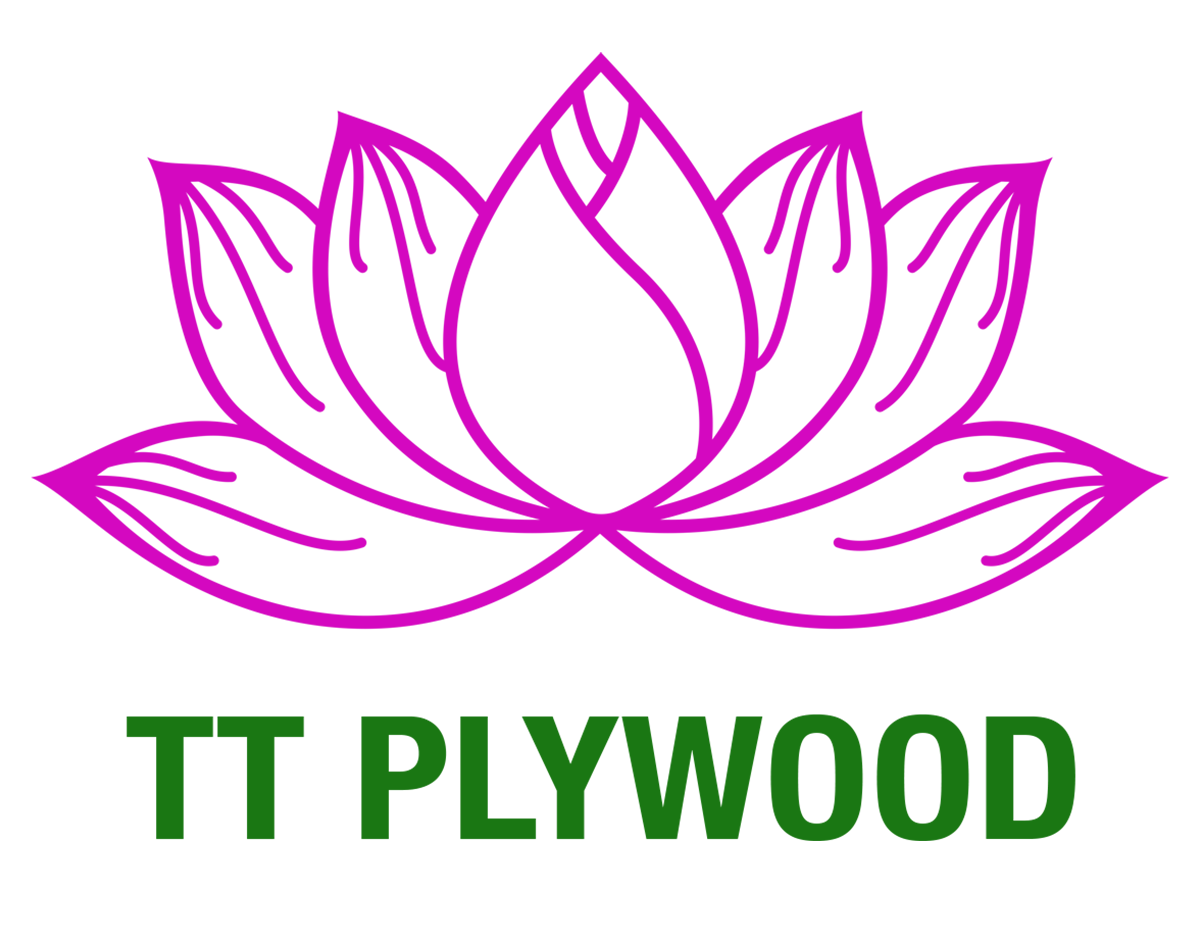
DIFFERENCES IN THE PLACEMENT PROCESS OF LVL AND COMMERCIAL PLYWOOD
Posted by Đỗ Tiến Hải at 09/11/2023
Scroll down to watch the production videos and view authentic factory photos from TT Plywood. See exactly how we stack core veneers for superior performance.
At TT Plywood, we understand that how you arrange the core veneers is just as important as the materials themselves. This article explores the differences in the core placement process between LVL (Laminated Veneer Lumber) and Commercial plywood, and how each method impacts the strength, durability, and end use of the panel.
What is LVL Plywood?
Laminated Veneer Lumber (LVL) is an engineered wood product made by stacking veneer layers in a single, parallel grain direction. The veneers are bonded under heat and pressure to create a high-strength, dimensionally stable panel. This structure makes LVL particularly suitable for load-bearing applications like beams, trusses, and structural framing.
What is Commercial Plywood?
Commercial plywood (MLH), often used for furniture, cabinetry, and interior structures, is made by layering veneers with alternating grain directions. This cross-laminated construction provides balanced strength in both directions, improving stability and resistance to warping.
How Core Placement Affects Performance
The stacking direction and method of the core veneers significantly influence how each type of plywood behaves under pressure, moisture, or cutting.
For LVL, veneers are aligned vertically in the same grain direction and secured with pins during production. This parallel arrangement allows for superior strength and rigidity, even when cut into smaller pieces. That’s why LVL is often chosen for heavy-duty structural components.
In contrast, the production of commercial plywood involves arranging veneers in horizontal, vertical, and sometimes H-shaped patterns to reduce overlap and ensure structural balance. While not as stiff as LVL, this method creates panels that are versatile and cost-efficient, perfect for general-purpose applications.
TT Plywood's Core Placement Process
At TT Plywood, both LVL and Commercial plywood are manufactured using precision machines and strict quality control. For LVL, the process involves moisture-controlled veneers, uniform stacking, industrial-grade adhesives, and high-pressure pressing. Commercial plywood follows a similar path but with more flexibility in veneer orientation and material grade, depending on the customer’s intended use.
LVL vs Commercial Plywood: Summary
Feature | LVL Plywood | Commercial Plywood |
---|---|---|
Grain orientation | Veneers are stacked in the same direction (parallel grain) | Veneers are cross-laminated (alternating grain direction) |
Core stacking method | Aligned vertically and pinned for structural consistency | Mixed horizontal, vertical, and H-pattern to balance internal stresses |
Strength & stiffness | Very high, ideal for beams and heavy-duty structures | Moderate, suitable for general interior and furniture applications |
Production complexity | Higher precision required, more layers involved | More flexible stacking, simpler lay-up |
Typical applications | Structural framing, load-bearing supports, large industrial packaging | Furniture, cabinetry, flooring substrate, decorative panels |
LVL offers consistent strength along one axis, ideal for structural use. Commercial plywood provides multi-directional stability and better workability, making it a go-to option for interior and furniture applications. The difference lies not in the material alone, but in how it’s arranged during production.
Real-World Applications
Both types of plywood have distinct advantages depending on the job. LVL is ideal for use in structural beams, door cores, or industrial-grade crates. Commercial plywood works well for furniture, flooring substrates, and light construction.
FAQ
What makes LVL stronger than commercial plywood?
Its unidirectional grain alignment gives it superior load-bearing capacity.
Can I use commercial plywood for structural purposes?
Only in non-load-bearing roles. For heavy-duty support, LVL is recommended.
Are both options available in moisture-resistant grades? Y
es. When bonded with phenol-formaldehyde adhesives, both can be made water-resistant.
Conclusion
Understanding the core placement process behind plywood production reveals why some panels are better suited for structural strength, while others excel in versatility and finish. At TT Plywood, we tailor our production approach to meet the specific performance needs of each product category.
Looking for plywood you can trust? Contact TT Plywood today to learn more or request a product consultation.
🤝For more detailed information, please contact us for the best products and most attractive prices. We will not let you down.
Hotline/WhatsApp/Line/Kakao: +84 326 942 288
Email: info@ttplywood.com
Website: https://ttplywood.com/
Tags :
birch plywood
box
cheap plywood
Commercial plywood
construction plywood
crate
EXPORT PLYWOOD
FFP
film faced plywood
frames
Furniture plywood
LVL
Marine plywood
packing plywood
pallet
pine face
plywood
PLYWOODVIETNAM
TTP
TTPLYWOOD
TT PLYWOOD
VENEER
Vietnamese plywood