-
-
-
Total payment:
-
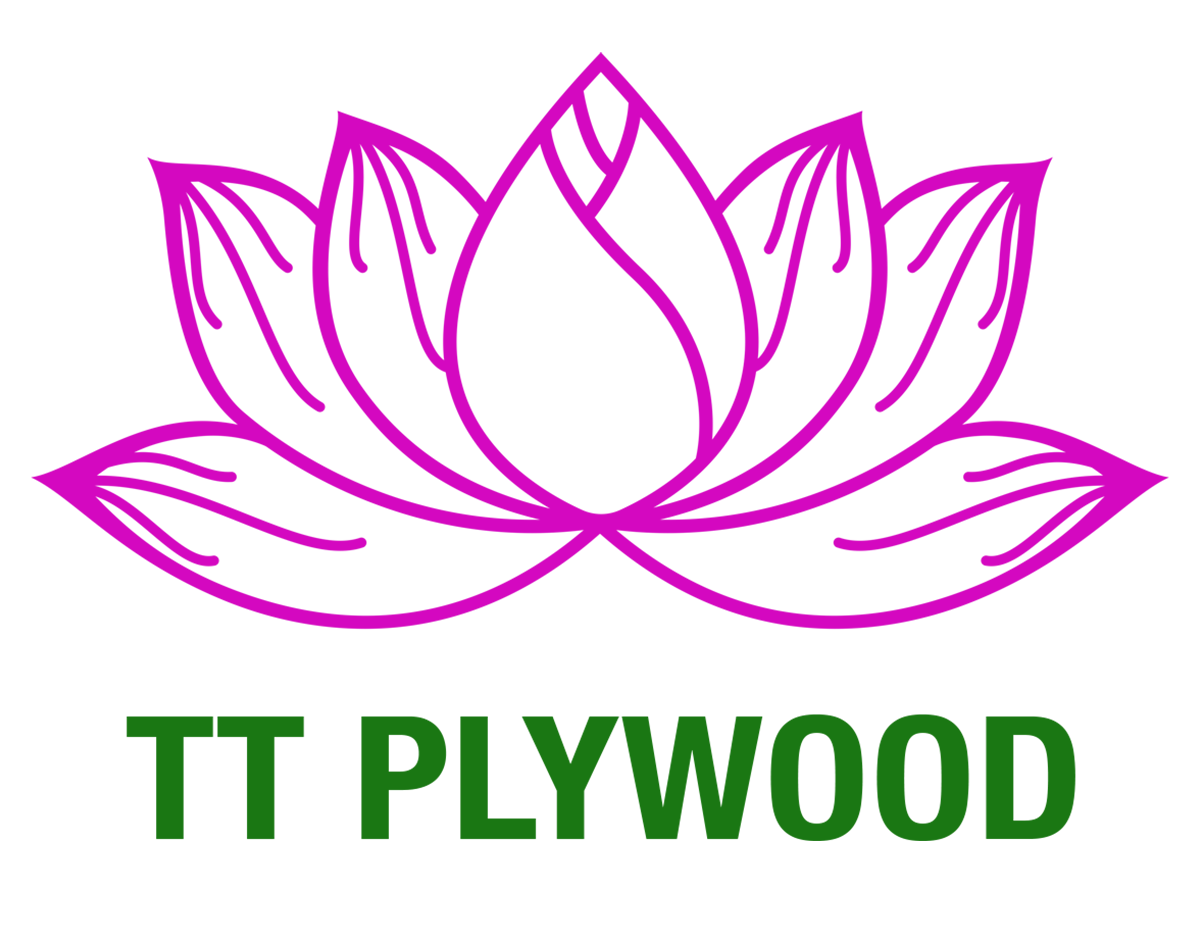
Manufacturing Process of Film Faced Plywood: A Step-by-Step Guide
Posted by Thanh Uyên at 22/04/2025
Film faced plywood is a high-quality construction material widely used in concrete formwork, flooring, and other structural applications. Its durability, water resistance, and smooth surface make it ideal for demanding construction projects.
In this article, we’ll break down the manufacturing process of film faced plywood in simple terms, ensuring even non-experts can understand how it’s made.
1. What is Film Faced Plywood?
Film faced plywood is a type of plywood coated with a phenolic or melamine film on both sides. This coating provides:
- Water resistance – prevents swelling and warping in wet conditions.
- Smooth surface – allows easy concrete demolding.
- Durability – withstands heavy loads and repeated use.
Now, let’s explore how it’s manufactured.
2. Step-by-Step Manufacturing Process of Film Faced Plywood
Step 1: Log Selection & Peeling
The process begins with selecting high-quality hardwood or softwood logs, typically eucalyptus, birch, or pine.
- Debarking: The logs are stripped of their bark.
- Peeling: The logs are rotated against a blade, producing thin wood veneers (0.2mm to 4mm thick).
Step 2: Veneer Drying
Freshly peeled veneers contain high moisture content (30-60%), which must be reduced to 8-12% for stability.
- Drying Method: Veneers pass through a hot air dryer at 160-180°C.
- Quality Check: Warped or cracked veneers are removed.
Step 3: Glue Application (Plywood Core Assembly)
The dried veneers are layered and glued to form the plywood core.
- Glue Type: Phenol-formaldehyde (PF) resin (waterproof) or urea-formaldehyde (UF) resin (indoor use).
- Layering: Odd-numbered layers (3, 5, 7, etc.) are stacked in cross-grain patterns for strength.
Step 4: Hot Pressing
The layered veneers are pressed under high heat and pressure to bond them permanently.
- Temperature: 120-150°C
- Pressure: 150-200 kg/cm²
- Time: 5-15 minutes (depending on thickness)
Step 5: Sanding & Trimming
The pressed plywood is sanded to ensure a smooth surface.
- Sanding: Removes rough spots for better film adhesion.
- Trimming: Cut to standard sizes (1220x2440mm, 1250x2500mm, etc.).
Step 6: Film Coating (Most Critical Step)A phenolic or melamine film is applied to both sides.
- Film Types:
- Brown Film – Standard, good durability.
- Black Film – Extra UV and weather resistance.
- Red Film – High-density, for heavy-duty use.
- Process:
- The plywood is pre-heated.
- Film sheets are placed on both sides.
- A hot press (140-180°C, 15-25 kg/cm² pressure) bonds the film.
Step 7: Cooling & Final Inspection
- Cooling: The plywood is cooled to stabilize the adhesive.
- Quality Checks:
- Thickness tolerance (±0.2mm)
- No bubbles or peeling film
- Edge sealing (optional for extra waterproofing)
Step 8: Packing & Shipping
- Packaging: Wrapped in plastic or steel straps to prevent moisture.
- Storage: Kept in dry conditions to avoid warping.
3. Key Quality Factors in Film Faced Plywood Production
To ensure high-quality film faced plywood, manufacturers must control:
- Core Veneer Quality – No gaps or overlaps.
- Glue Quality – Waterproof phenol resin for long-lasting bonds.
- Film Adhesion – No peeling under heat and moisture.
- Press Control – Proper temperature and pressure for strong lamination.
4. Applications of Film Faced Plywood
Due to its strength and water resistance, film faced plywood is used in:
- Concrete formwork – Reusable shuttering for walls, columns, and slabs.
- Flooring & roofing – Sturdy base for heavy loads.
- Scaffolding boards – Slip-resistant and durable.
5. Conclusion
The manufacturing process of film faced plywood involves log selection, veneer peeling, gluing, pressing, film coating, and quality checks. Each step ensures the final product is strong, waterproof, and long-lasting.
When choosing film faced plywood, always check:
✔ Film type (phenolic/melamine)
✔ Core material (birch, eucalyptus, or mixed)
✔ Glue quality (WBP glue for waterproofing)
By understanding the production process, you can select the best film faced plywood for your construction needs.
Frequently Asked Questions (FAQs)
Q: How many times can film faced plywood be reused?
A: High-quality plywood can last 20-50 uses depending on care and concrete pressure.
Q: What’s the difference between black and brown film?
A: Black film has better UV resistance, making it suitable for outdoor projects.
Q: Can film faced plywood be used for furniture?
A: Yes, but it’s mainly designed for construction formwork due to its rough texture.
Contact us today for the latest pricing and sourcing options!
📞Hotline/WhatsApp/Line/Kakao: +84 32 694 2288
📧Email: info@ttplywood.com
🌐Website: https://ttplywood.com/
LinkedIn: https://www.linkedin.com/in/tt-plywood/