-
-
-
Total payment:
-
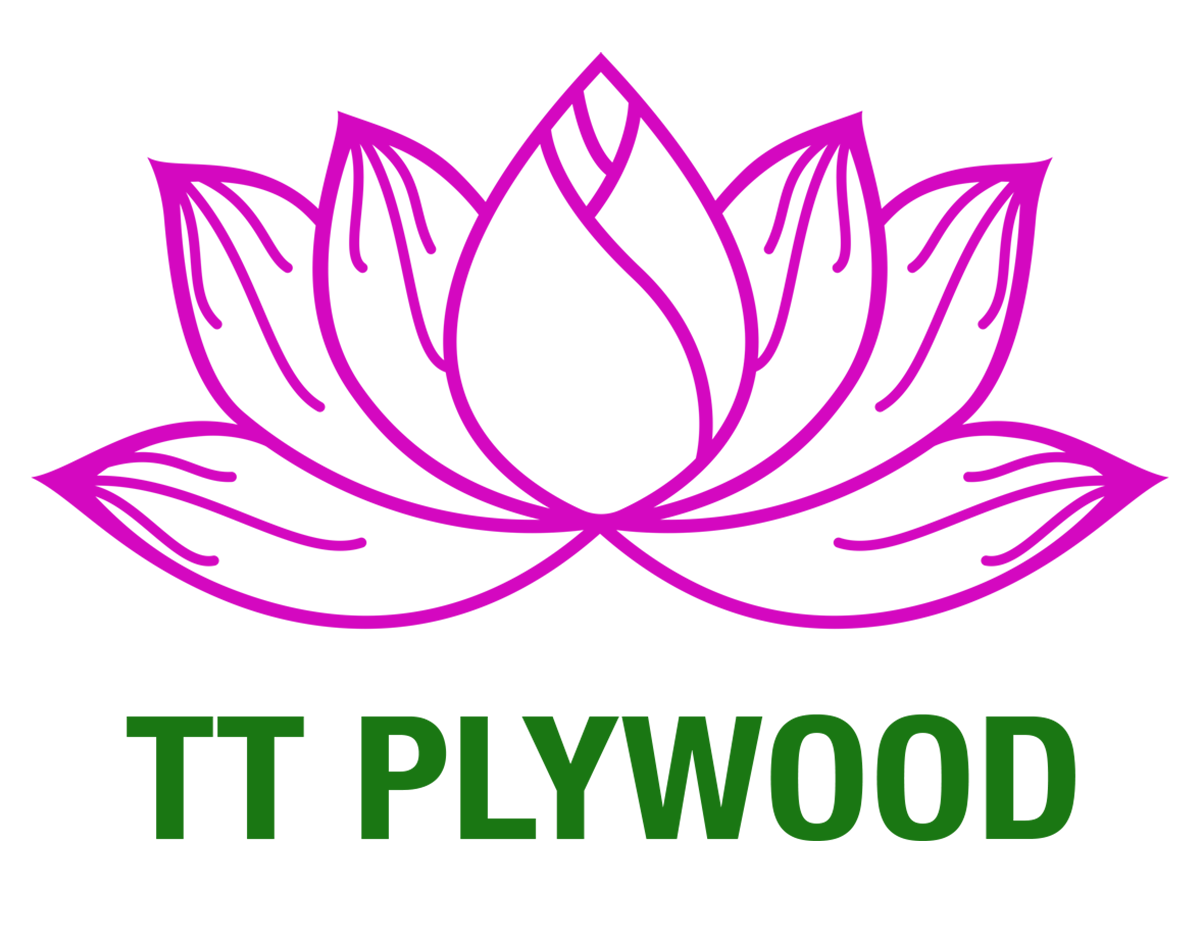
Plywood in the automotive industry
Posted by Kiều Trang at 07/11/2024
In the automotive industry, choosing the right materials not only impacts the quality of the product but also affects production costs and vehicle performance. One material that is increasingly being used in car manufacturing and maintenance is plywood. With its superior durability, load-bearing capacity, and high flexibility, plywood is gradually replacing traditional materials, helping to optimize production processes and protect vehicle components.
Why Plywood Is Used in the Automotive Industry
1. Durability and load-bearing capacity
Plywood is made from several thin layers of wood glued together, creating a strong panel. This allows plywood to withstand heavy loads and impact, making it crucial for producing automotive parts such as shields, dashboards, car frames, and interior components.
2. Cost reduction and production optimization
Plywood is easy to work with and flexible, helping automotive manufacturers save costs and time during production. Using plywood instead of other materials like metals or plastics not only reduces costs but also lowers the overall weight of the vehicle, thereby improving fuel efficiency and performance.
3. Applications in automotive interior components
Plywood is widely used in producing automotive interior parts like dashboards, car doors, seat frames, trim panels, and decorative details. These components not only require high durability but also need to withstand heat, humidity, and resist warping over time. Plywood meets these requirements and adds a sleek, elegant look to the vehicle interior.
4. Moisture and termite resistance
Plywood’s resistance to moisture and termites makes it suitable for use in damp environments, such as undercarriage components, protective shields, or storage area panels. This helps protect vehicle parts from environmental damage.
Applications of plywood in the automotive industry
1. Production of interior parts
Plywood is used to produce various parts such as seat frames, dashboards, dividers, soundproofing panels, and decorative interior details. Not only does plywood make these parts durable, but it also enhances the aesthetic appeal of the vehicle's interior.
2. Protecting underbody components
Plywood is used in manufacturing protective components under the car, such as engine shields, fuel tank covers, and exhaust system parts. Its ability to withstand impact and environmental conditions ensures effective protection of these components throughout the vehicle’s operation.
3. Manufacturing lightweight automotive parts
Plywood can replace other materials in producing lightweight automotive components like shields, engine covers, and cabin panels. Due to its light weight, plywood helps reduce the vehicle’s overall weight, contributing to better fuel efficiency and improved vehicle performance.
Benefits of using plywood in the automotive industry
1. Cost savings in production
Plywood is cheaper than many other materials, such as metals, and it is easy to process and customize to specific production needs. This helps companies save on manufacturing costs and improve overall production efficiency.
2. High flexibility
Plywood can be easily shaped, bent, and cut into complex shapes, offering high creative potential for designing automotive parts. Car designers can take advantage of plywood’s flexibility to create unique and innovative vehicle components.
3. Environmental protection
Plywood is made from natural wood layers, which are recyclable and easy to dispose of after use, helping reduce negative environmental impacts. Using plywood instead of non-recyclable materials like plastics or metals helps the automotive industry meet sustainability standards.
Plywood has proven to be a useful and versatile material in the automotive industry, from producing interior parts and vehicle components to protecting underbody parts. With its ease of processing, high durability, and cost-effectiveness, plywood helps automotive manufacturers optimize production processes, reduce costs, and enhance vehicle performance.