-
-
-
Total payment:
-
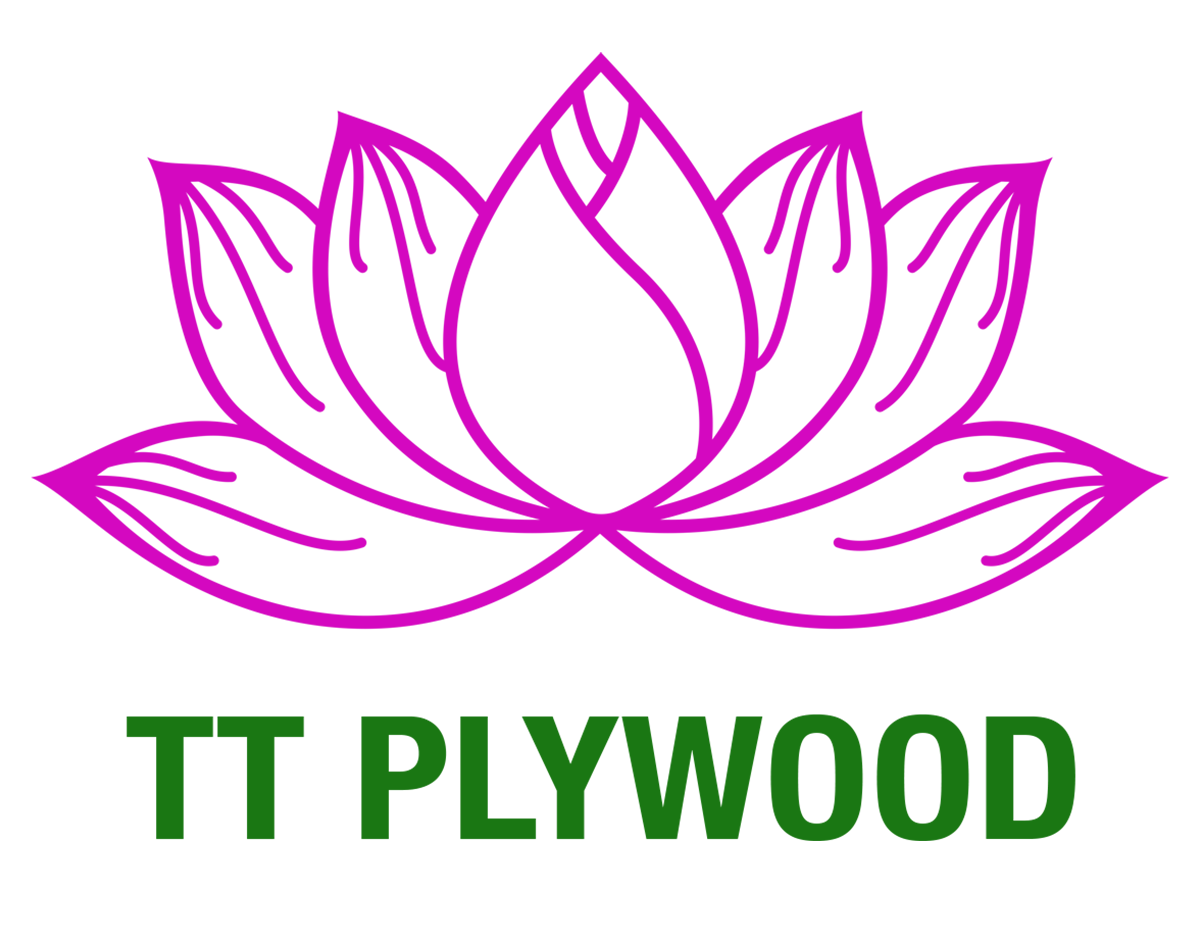
Understanding Film-Faced Plywood Grades: AA, BB, and CC – A Complete Guide
Posted by Thanh Uyên at 03/04/2025
( Film-faced plywood)
Film-faced plywood has become an indispensable material in modern construction projects worldwide. Its unique combination of strength, durability, and moisture resistance makes it particularly valuable for concrete formwork applications. However, not all film-faced plywood is created equal. The grading system – AA, BB, and CC – serves as a crucial indicator of quality, performance, and suitability for different construction scenarios.
In this comprehensive 2000+ word guide, we'll dive deep into:
- The fundamental characteristics of film-faced plywood
- Detailed breakdowns of AA, BB, and CC grades
- Real-world applications and case studies from global projects
- Expert recommendations for selecting the right grade
- Maintenance and optimization tips
- Emerging trends in plywood technology
What Makes Film-Faced Plywood Special?
Before examining the grades, it's essential to understand what sets film-faced plywood apart from regular plywood:
Core Composition
Film-faced plywood typically features:
- Hardwood core (birch, poplar, or eucalyptus) for superior strength
- Multi-layered cross-grain construction for dimensional stability
- High-density core materials that resist warping
Protective Film Layer
The phenolic or melamine resin coating provides:
- Exceptional water resistance (can withstand prolonged exposure)
- Chemical resistance to concrete alkalinity
- Smooth surface for easy demolding
- UV protection for outdoor applications
- Abrasion resistance for multiple reuses
Performance Advantages
Compared to traditional plywood, film-faced versions offer:
- 3-5 times longer service life
- Consistent concrete surface quality
- Reduced labor costs for surface finishing
- Lower total cost per use cycle
Decoding the Grading System: AA, BB, and CC
The grading system primarily reflects the quality of surface veneers and film coating. Here's a detailed examination of each grade:
AA Grade: The Premium Choice
Specifications:
- Face Side: Flawless phenolic film with no visible defects
- Back Side: Equally high-quality finish
- Core Material: 100% hardwood (often birch)
- Glue Type: WBP (Water Boil Proof) phenolic resin
- Thickness Tolerance: ±0.2mm
Performance Characteristics:
- Reusability: 30-50 cycles with proper care
- Concrete Finish: Mirror-smooth surface (Ra < 3.2μm)
- Moisture Content: 8-12% (optimized for dimensional stability)
Global Case Study: Burj Khalifa, Dubai
The world's tallest building utilized AA-grade film-faced plywood for its critical formwork systems. The material's consistent performance under extreme desert temperatures and its ability to maintain precise tolerances contributed to the project's success. Over 12,000 sheets were used, with many achieving 40+ reuses.
BB Grade: The Balanced Performer
Specifications:
- Face Side: Minor defects allowed (small knots ≤5mm)
- Back Side: Slightly more visible imperfections
- Core Material: Mixed hardwood (often poplar core)
- Glue Type: MR (Moisture Resistant) or WBP
- Thickness Tolerance: ±0.5mm
Performance Characteristics:
- Reusability: 15-25 cycles
- Concrete Finish: Slightly textured (Ra 6.3-12.5μm)
- Moisture Content: 10-14%
European Case Study: Crossrail Project, London
Europe's largest infrastructure project strategically used BB-grade plywood for most tunnel formwork. The material provided an optimal balance between cost and performance, with an average reuse cycle of 18 times across the project's 42km of new tunnels.
CC Grade: The Economical Solution
Specifications:
- Face Side: Visible defects (knots ≤15mm, repaired areas)
- Back Side: Significant imperfections acceptable
- Core Material: Often softwood or mixed composition
- Glue Type: MR or lower-grade adhesives
- Thickness Tolerance: ±1.0mm
Performance Characteristics:
- Reusability: 5-10 cycles
- Concrete Finish: Rough surface (Ra > 25μm)
- Moisture Content: 12-18%
Asian Case Study: Mumbai Metro Project
The extensive metro network construction utilized CC-grade plywood for initial foundation works and temporary structures. This approach reduced material costs by 35% compared to using higher grades, while still meeting structural requirements for non-visible concrete elements.
Technical Comparison Table
Parameter |
AA Grade |
BB Grade |
CC Grade |
Surface Quality |
Mirror finish |
Slight texture |
Visible defects |
Core Density |
≥680kg/m³ |
620-680kg/m³ |
≤620kg/m³ |
Bending Strength |
≥50MPa |
40-50MPa |
30-40MPa |
Water Absorption |
≤5% in 24h |
5-8% in 24h |
8-12% in 24h |
Price Premium |
+40-60% |
Baseline |
-20-30% |
Selecting the Right Grade: A Decision Matrix
Use this expert framework to determine the optimal grade for your project:
1. Project Duration
- Short-term (<6 months): Consider CC
- Medium-term (6-18 months): BB preferred
- Long-term (>18 months): Invest in AA
2. Budget Constraints
- High budget: AA for all applications
- Moderate budget: AA for critical areas, BB/CC elsewhere
- Tight budget: Strategic use of BB with CC for non-critical uses
3. Environmental Conditions
- Extreme weather: AA performs best
- Moderate conditions: BB suitable
- Controlled environments: CC can work
Maximizing Plywood Performance: Maintenance Tips
Regardless of grade, proper care extends service life:
1. Cleaning Protocol
- Remove concrete residue within 24 hours
- Use plastic scrapers (never metal)
- pH-neutral cleaners for film protection
2. Storage Best Practices
- Stack horizontally on level surface
- Cover with tarpaulin in outdoor storage
- Maintain 10cm ground clearance
3. Repair Techniques
- Small damages: Apply epoxy filler
- Edge wear: Seal with polyurethane
- Film delamination: Professional recoating possible for AA/BB grades
Emerging Trends in Film-Faced Plywood
The industry is evolving with several innovations:
1. Hybrid Core Technology
- Combination of hardwood and synthetic materials
- 20% lighter with equal strength
- Pioneered by Scandinavian manufacturers
2. Smart Coatings
- Nano-treated films with self-cleaning properties
- Color-changing indicators for wear detection
- Being tested in German automotive plants
3. Sustainable Options
- FSC-certified cores
- Low-formaldehyde adhesives
- Recyclable film layers
Common Mistakes to Avoid
1. Grade Misapplication
- Using CC for architectural concrete
- Over-specifying AA for temporary works
2. Improper Handling
- Dropping sheets from height
- Exposure to direct sunlight for extended periods
3. False Economy
- Choosing cheap imports without proper certification
- Ignoring total cost per use calculation
Global Standards and Certifications
Reputable manufacturers comply with:
- EN 636 (European standard)
- JIS K 6802 (Japanese standard)
- GB/T 17656 (Chinese standard)
- ASTM D3043 (American standard)
Always request test certificates for:
- Formaldehyde emission (E0 or E1)
- Bonding quality
- Bending strength
Conclusion: Making the Right Choice
Understanding film-faced plywood grades is more than just recognizing surface differences—it's about matching material capabilities to project requirements for optimal performance and cost-efficiency.
As construction methods evolve and sustainability becomes increasingly important, the intelligent specification of film-faced plywood will continue to play a crucial role in successful project delivery worldwide.
Final Recommendation: Consult with technical specialists from reputable manufacturers to conduct a proper cost-benefit analysis for your specific application. Many leading suppliers now offer lifecycle cost calculators to help optimize your material selection.