-
-
-
Total payment:
-
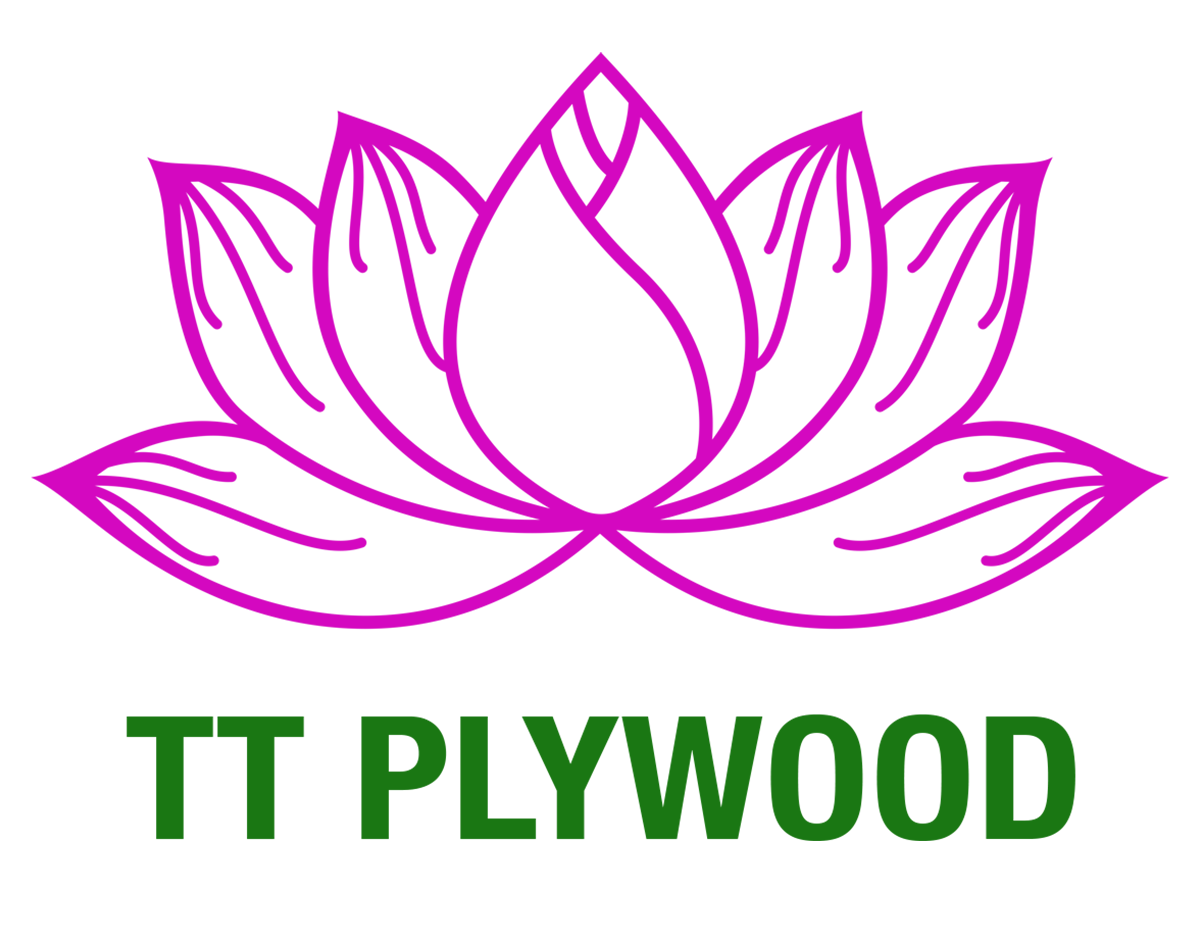
Advanced technology in film-faced plywood production
Posted by Kiều Trang at 08/10/2024
Advanced technology is increasingly being emphasized in the production of film-faced plywood. Modern technologies help increase production efficiency and enhance product quality. Below are some advanced technologies used in the production of film-faced plywood:
1. Thermal Press Technology
- Utilizing modern thermal presses with precise control over temperature and pressure helps improve the durability and properties of plywood.
- Hot Pressing
- After completing the stacking process (typically, workers stack 12-15 sheets at a time, equal to the number of slots in the hot press. For thinner sheets, 2 sheets may be pressed in 1 slot, allowing for 24-30 sheets per round), the stacked plywood is placed into the press. Depending on the thickness of the sheets, either 1 sheet or 2 sheets can be placed per tray.
- The press will begin compressing the sheets together. The pressure and temperature settings depend on the thickness of the plywood (with slight variations based on the machine). Typically, pressing time is around 30-40 minutes at a temperature of about 130°C.
- During pressing, workers will release and rotate the sheets once to ensure even pressing on both sides, preventing one side from becoming too hot while the other remains insufficiently heated.
- After pressing, the sheets are removed from the press and stacked in slots to cool. Cooling is critical for shaping the sheets and reducing warping.
- Cold Pressing
- The sheets are then placed into a cold press for 3-6 hours, depending on weather conditions, to achieve preliminary shaping and strengthen the internal structure.
2. Automatic Film Coating Technology
- Automatic film coating systems ensure an even application, minimize defects, and save materials. Modern spraying or laminating technologies allow for diverse, high-quality surfaces.
3. Infrared Drying Technology
- Infrared drying systems accelerate the drying process of plywood, improving production efficiency without compromising product quality.
4. Sensors and Automation
- Sensors are used to monitor parameters such as temperature, humidity, and pressure throughout the production process, allowing for automatic adjustments that optimize product quality.
5. Automatic Quality Inspection Machines
- Modern quality inspection machines can detect surface and coating defects, ensuring products meet standards before shipment.
- Before moving to the final packaging stage, the QC team conducts quality checks on the plywood. The product goes through two steps (two pairs of selections), including surface inspection, moisture, thickness, dimension checks, and structural assessments. Particularly for sheets thicker than 11mm, workers must use a wooden mallet to tap and check for any delamination in the plywood structure.
6. Production Management Software
- The implementation of ERP software helps track and manage the entire production process, from planning and inventory control to data analysis, optimizing workflow.
7. Recycling and Environmental Protection Technology
- Utilizing recycled materials and environmentally friendly production processes helps minimize waste and energy consumption.
8. Digital Printing Technology
- Digital printing technology is used to create diverse designs and patterns on the surface of plywood, expanding customization options for products.
Advanced technologies in film-faced plywood production not only enhance production efficiency but also improve product quality, meeting the increasingly high demands of the market. The adoption of these technologies will provide significant competitive advantages for manufacturers
Tags :
advanced technology
digital printing
film faced plywood
heat press
infrared drying
quality check
sensor
TT PLYWOOD