-
-
-
Total payment:
-
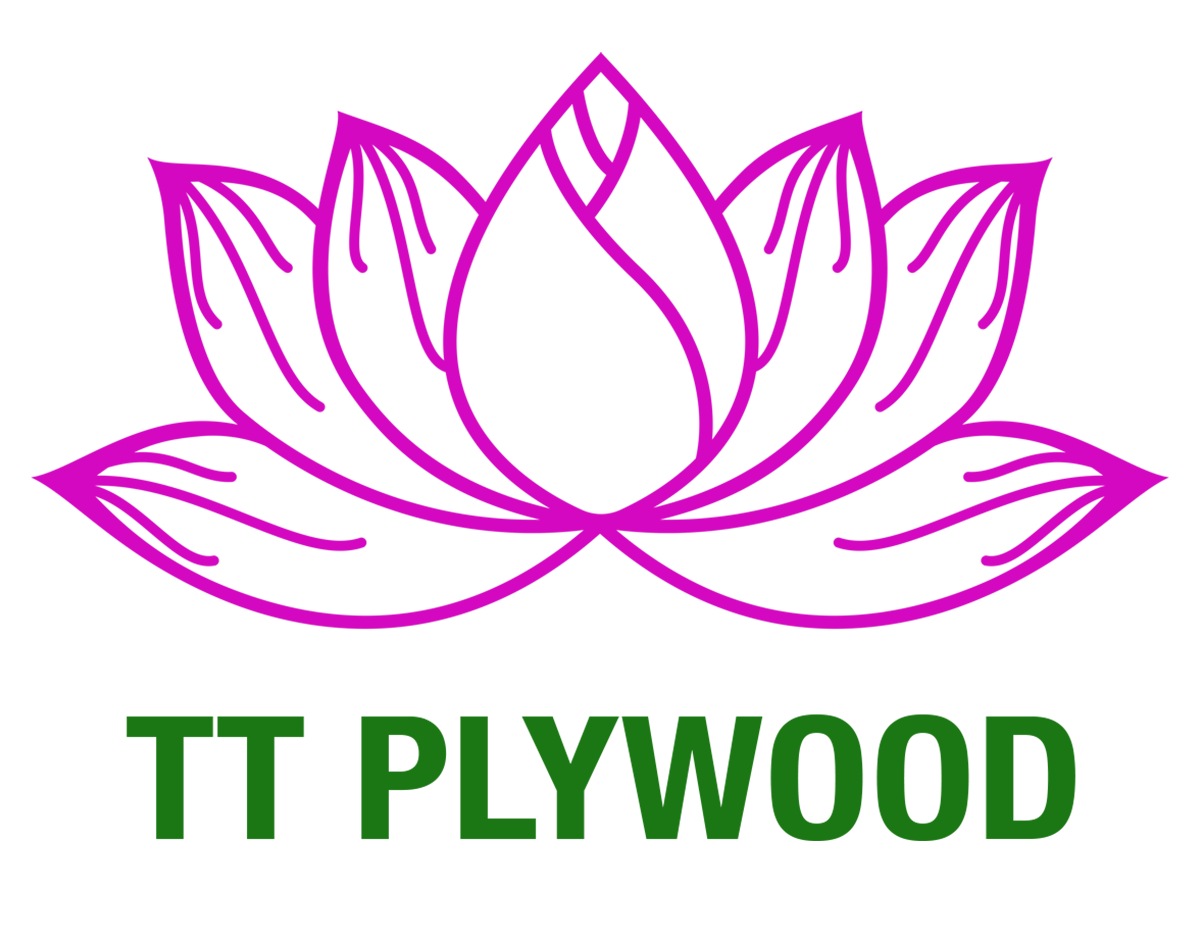
Detailed process of modern film-faced plywood production
Posted by Kiều Trang at 01/10/2024
To produce a complete film-faced plywood product under the TT PLYWOOD brand that meets high quality standards, not only the process of selecting raw materials is important, but the production process also plays a significant role in ensuring product quality. We invite you to explore the production process of TT PLYWOOD film-faced plywood:
DETAILED PROCESS OF PRODUCTION OF FILM-COATED PLYWOOD
1. Raw Material Preparation:
Select the raw wood (commonly acacia, eucalyptus, or other types of wood).
Cut the wood into small strips and dry it to achieve the appropriate moisture content.
2. Wood Slicing:
Use a wood cutting machine or saw to slice the wood into thin layers (usually about 2-3mm thick).
3. Glue Preparation:
Prepare specialized glue (commonly phenolic or melamine glue) to bond the wood layers.
4. Layer Stacking:
Stack the glued wood layers in the correct order (usually with a hard wood layer on the outside and a soft wood layer in the middle).
5. Hot Pressing:
Place the stacked layers into a press machine with high temperature and pressure to bond the glue and form the plywood.
6. Cutting and Shaping:
After pressing, cut the plywood to the required dimensions and shape if necessary.
7. Film Facing:
Apply a protective film layer on the surface of the plywood to enhance durability and water resistance.
8. Drying:
Dry the plywood to ensure the glue has completely cured and to reduce the moisture content of the product.
9. Quality Inspection:
Conduct quality checks to ensure there are no defects and that the product meets quality standards.
10. Packaging and Shipping:
Pack the product to protect it during transportation and distribution.
This process is carried out by the team of workers at TTPLYWOOD to ensure the quality of the product when it reaches customers.