-
-
-
Total payment:
-
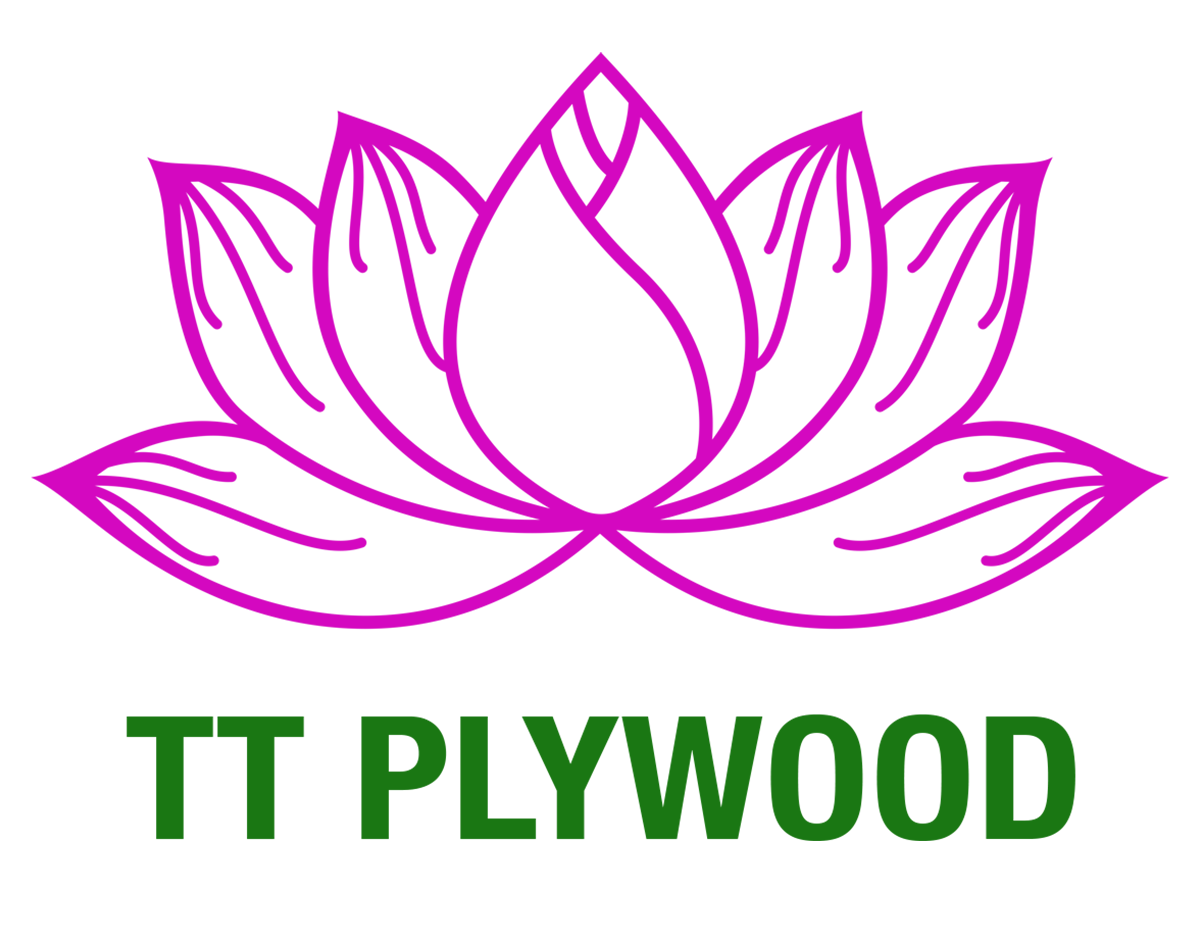
Production Process Commercial Plywood
Posted by Đỗ Tiến Hải at 04/08/2022
Commercial plywood is a noun that business people, manufacturers often call to refer to a type of board that is more advanced than ordinary plywood (packaging board). The difference lies in both the production process and the selection of raw materials.
Different from ordinary plywood, commercial plywood usually has a higher quality glued side, often called A face, Bintangor, Okoume, Pencil cedar, or oval face (rare). The glue used in this type of plywood will usually be E2 fine glue, after the face is glued, it will be smooth, so many people also call this type of board "scrub".
Basically quite similar to ordinary plywood but more detailed in some stages such as materials and finishing. Below is the production process of commercial plywood, also known as scrub, commercial. Basically, the first 4 steps of commercial plywood and packaging plywood are the same, only differing in the materials used:
- Select hardwoods such as acacia, eucalyptus, and linden, peeled and cut into appropriate lengths.
- The pieces of wood are put into the peeling machine to create the desired size and thickness of the filler (filler is also divided into many types: A, B, C)
- Dry the filler: can be dried in nature or use a dryer. In Vietnam, the climate is hot and humid, so many manufacturers often choose the outdoor drying method to save energy
- Rotate glue or glue strips: Usually, manufacturers will use glue machines to spread the glue evenly on both sides of the filler sheet
- Filling this step is usually manual, the thickness of the board is usually determined by this step. In turn, it will be a thin peeled board as a vertical filler, followed by a horizontal turn to make the sturdy board the most solid, then vertical, staggered like that until they reach the thickness that they need. we need.
- Cold pressing this step will help shape the board and bind the filler layers together.
- After being cold pressed, the board will be transferred to a hot press so that the structure of the board is strong
- Plywood will be put into the sander to smooth the surface
- Apply glue on both sides of the board and glue the face and then put it into hot press to complete the board
- The final step is to cut the board as required, choose to remove the defective goods and pack it for the customer
Above are 10 basic steps to form a commercial plywood in our factory. Indeed, to have a good plywood board to fully meet the needs of customers is not simple at all, isn't it? But above all we know we always need to work on improving our production lines, improving product quality, finding good solutions for the environment and reducing costs to be able to compete better.
If you are interested in plywood, please don't hesitate to contact us: Hotline/WhatsApp/Line/Kakao: +84 866 969 398 / +84 934 482 488 Email: sales@ttplywood.com Fanpage: TT Plywood Instagram: tt_plywood Website: https://ttplywood.com/ Alibaba: https://ttplywood.trustpass.alibaba.com/
See more: BENEFITS OF PLYWOOD - 10 OF THE BIGGEST BENEFITS OF PLYWOOD
Tags :
birch plywood
box
cheap plywood
Commercial plywood
construction plywood
crate
EXPORT PLYWOOD
FFP
film faced plywood
frames
Furniture plywood
LVL
Marine plywood
packing plywood
pallet
pine face
plywood
PLYWOODVIETNAM
tego
TTP
TTPLYWOOD
TT PLYWOOD
types of plywood
VENEER
Vietnamese plywood